It is very likely that at some point or another, one would have stopped to admire some rather unique structures – the Malta Freeport Warehousing, Playmobil, St. James Cavalier and more recently the Esplora Planetarium which epitomises creativity when coupled with technology in all forms. These structural masterpieces – or elements added onto, or supporting them – are the work of none other than the pioneering Pillow Space Frames Ltd.
Backed by years of experience in the business, this company has not only embellished our shores but has gone further afield. Design & Build has had the opportunity of speaking with the founder of Pillow Space Frame, Martin Pillow.
T o the uninitiated, space frames are three dimensional, rigid, lightweight, truss-like structures constructed from interlocking struts in a geometric pattern. Space frames are generally used to span large areas with few interior supports. The most recent and perhaps most recognised project is the Esplora Interactive Science Centre in Bighi. Esplora showcases the wide range of talents the company has – from design capabilities to project management and co-ordination. And despite Pillow Space Frame having an impressive portfolio which stretches far beyond Malta’s shores, this was nonetheless a marvelously herculean project; the complexities and intricacies required to execute it were immeasurable.
Humble Beginnings
Perhaps few are aware that the catalyst behind Martin’s drive and passion for hard work was the death of his ten-year-old sister Maria, who had tragically lost her life in a traffic accident in Sliema in 1964. Crossing the road after buying bread for the family, she got hit by a car and succumbed to her injuries five days later. Maria’s death proved to be a great blow, particularly for her parents. Martin was determined to pull his family through the tragedy, and he lost himself in work, subsequently falling in love with his labour.
In 1974, the company started exporting to Libya
Pillow Space Frame’s origins thus go back to humble beginnings when in the 1960s, Martin Pillow started dabbling in wrought iron works. Hailing from a large family, Martin was the eldest male of ten siblings. After gaining what were the equivalent of Advanced Levels at that time, Martin immediately set to work producing wrought iron for some of Malta’s richest families. Working from what was referred to as a Casa Bottega – a workshop which was constructed in the back garden of the Pillow family home, for most of the time, his brothers were involved in the work that was being produced.
History In The Making
In the early 70s, as work started to increase, Martin approached the now defunct Malta Development Corporation in the hope of securing premises in Bulebel. This unfortunately never really materialised – possibly due to the modest size of the business at the time. In November 1972 the Labour Government – one year into power, was requisitioning property from the British Forces. This exercise by Prime Minister Dom Mintoff resulted in the acquisition of two Nissen huts in Corradino for which a two hundred Maltese Lira annual rent was paid. Subsequently, in 1974, the company started exporting to Libya.
After years of operation that involved members of the family, 1988, Martin bought his father’s share of the company to eventually become its sole owner. The business has now been around for approximately fifty years and has evolved through time – starting off with aluminium apertures and finishes and moving on to projects that are more specialised. The company’s pursuit of innovation was the reason for them to move on from the generic and mundane business of aluminium towards more specialised infrastructures, some of which are now nearing their third decade of existence.
in a record of 5 months it designed and manufactured the largest Hangar of 100 x 50 metres for Medavia at Safi Aviation Park
Pillow Space Frame was formed in 1990 with the aim of executing the first ever space frames in Malta, specifically constructed for the first of ten warehouses of 1,000 m2 each for the Malta Freeport. By the year 2000 the Company was handling the Playmobil Factory at Hal Far, the glazed domes of the National Art Centre at St James Cavalier, and the second hangar 50 x 50 meters for Medavia in Tripoli Libya. Another milestone acquired by the Company was in 2010 when in a record of 5 months it designed and manufactured the largest Hangar of 100 x 50 metres for Medavia at Safi Aviation Park.
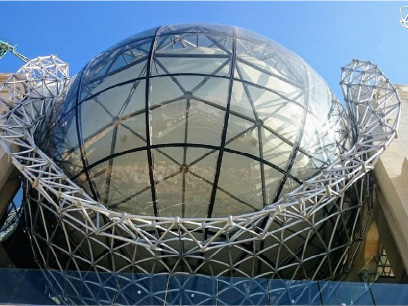
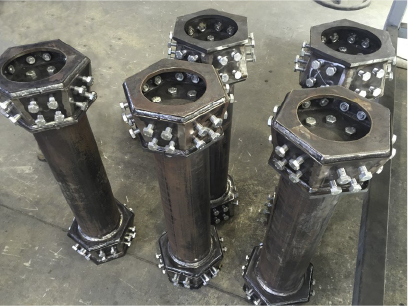
(left) the Double-layer 3-frequency icosahedral geodesic dome created and installed by Pillow Space Frames at the Esplora Planetarium (right) the special double nodes that connect the dome’s only 3 supports to the columns
The year 2012 was yet another milestone for the Company as it manufactured and exported space frame structures for the Venezuelan Government in Caracas. In total Pillow Space Frame completed 7 train stations. In 2015 the Company executed a 7,000 m2 Space Frame roofing for a recycling plant in Gozo, and in 2016 finished ‘Esplora Planetarium’, ‘The Monumental Staircase’, ‘Spiral Staircase’ and the ‘Veil Structure’ at the Science Centre at Bighi.
Pillow Space Frames conceptualise, design and create mechanical infrastructures built to outlast more traditional solutions
The Quality Concept
When choosing material for the project being undertaken, it all comes down to the requirements of the task at hand. For example, when one selects a beam it has to go through a process of structural design. The choice is always a two way conversation between Pillow Space Frames as fabricators and the structural engineers. This two way approach is important to ensure that the conceptual design is of quality. When it comes to sourcing of materials, Pillow Space Frames have a long standing relationship with a number of Italian suppliers – the choice of such was based on both sharing the same values of passion and quality towards their work as well as having good pricing structures and quick transport delivery times.
Pillow Space Frames also collaborates with architects, structural engineers project managers. A way of summing up their unique core competences is that Pillow Space Frames conceptualise, design and create mechanical infrastructures built to outlast more traditional solutions.
They are equally comfortable in executing those plans requested by the architectural and engineering professionals they team up with.
Esplora Interactive Science Centre – Bighi
The Esplora Interactive Science Centre in Bighi, can be considered to be one of the main flagship projects of the company. The involvement came about when C&F Contractors, winners of the public tender, brought in Pillow Space Frame to install specialised steel works with curved glass.
Of course, the elaborate process kicked off in the quotation stage which was a complex process in itself. This was because the company had to come up with figures for a non-standard construction.
Thus, the actual execution of the project kicked off with the structural design and planning. The recognisable, innovative dome and the way it is connected to the steel frame presented a very interesting structural concept where the configuration is wholly supported on three complex points designed by Martin Pillow himself.
As happens with all projects, numerous phases had to be completed. The most interesting phases were the fabrication and installation of custom made nodes. Following rigorous testing, the cladding process followed – this involved the installation of prefabricated multiple layers insulated with internal acoustic panels and installed on site.
Not many entities – if any at all beyond Pillow Space Frame, who could execute such complex requirements with such finesse, would come to mind
The double curved glass was another major challenge since there are very few manufacturers that can achieve such double curved glass at this level of quality and accuracy. The glass had to be sourced from abroad. And it is far from delivered to be utilised ‘ready out of the box’.
A custom extrusion system of glass adhesion had to be meticulously planned – this intricate exercise involved adhering glass to glass, with aluminium components – custom made by Pillow Space Frames – sandwiched in between.
The assembled glass was thus then returned to Italy following Pillow Space Frame’s intervention, to be completed according to the specifications given.
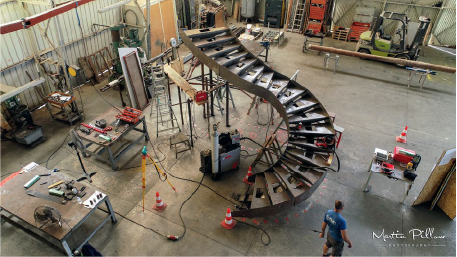
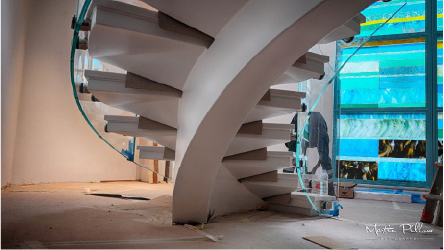
Pillow Space Frames also manufactures custom construction, structural and internal solutions for residential and commercial buildings and developments.
The final element to the project was the installation of the external veil, which is of freeform geometry. At project initiation, it was thought to be almost impossible to create, given that it had to be installed on site, requiring very specific lifting techniques.
The complexity of this installation was further exacerbated by the fact that the dome and glass were already in place. In terms of technical specification, the dome caters for a maximum loading of 280 tons of vertical loading, resting on three concrete columns. The installation was implemented at difficult angles with manoeuvring and hoisting proving to be very difficult. Not many entities – if any at all beyond Pillow Space Frame, who could execute such complex requirements with such finesse, would come to mind. Such an installation requires a high level of competence required not solely by key individuals, but by the entire team, complementing each other; on such project executions.
Steel gives so much architectural freedom. When utilised correctly and designed for full optimisation, installation turnaround times are far quicker than those of concrete buildings, making steel far more economical and therefore cost effective
Changing Environments
With the changing environment in the construction industry, Malta is focusing on higher buildings and smaller footprints resulting in every square centimetre being vital. How is Pillow Space Frame being of service through the installation of steel in buildings, designed to Malta’s new construction requirements?
In reality, the industry is still very much fascinated with concrete. But when you see the consequences of that, no one realises that it is a very heavy building element. The question being posed is: is concrete safer and longer lasting than steel?
The answer is a resounding ‘No’. Once steel is structurally designed, then it is fit for purpose. If protected correctly then steel does not have a relative shelf life – this is because it is installed internally into the building and therefore not exposed to corrosive environments, and to natural elements such as seismic activity.
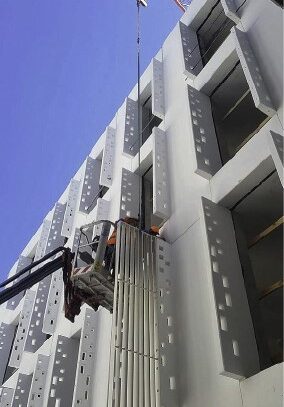
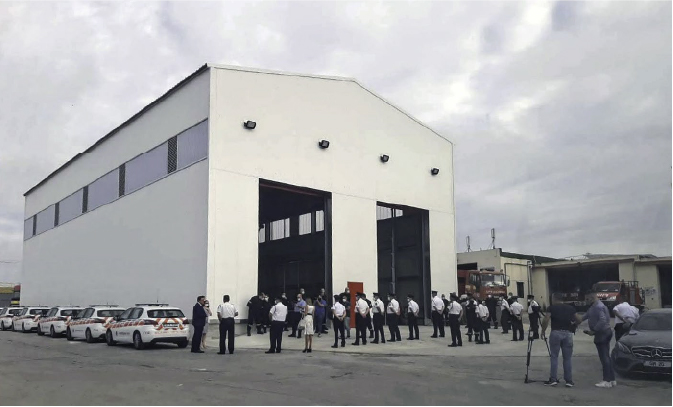
Being so light, steel creates a less seismic load. An example of a country aptly using this material is Japan, where due to the seismic nature of their country, their architects ensure that their buildings are as light as possible.
Waxing lyrical about the benefits of the usage of steel in the construction industry begs the question – Is it being used in Malta?
the roof is made up of a space frame clad with concrete – this has enabled the facility to integrate seamlessly within its landscape as well as sustain very high loads
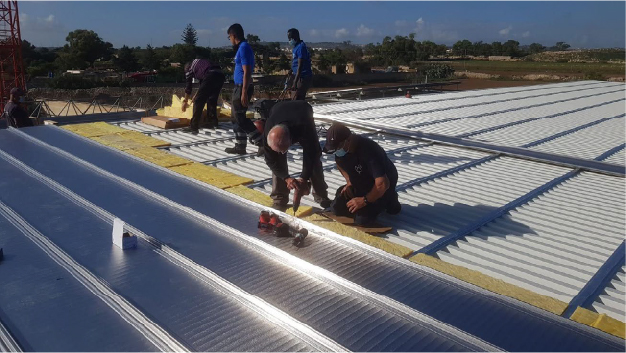
Typically, steel is used more in industrial projects – Aircraft hangars, and factory and manufacturing spaces are two of the major recipients of Pillow Space Frame’s labour. Another benefit of such installations is the fact that Pillow Space Frames can easily construct column-free manufacturing spaces with spans of 90 meters – examples of when this comes in handy are when gantry cranes are to be used, or for large conference areas; such is where steel literally shines!
The Playmobil factory is a case in point. The factory structure is made up of a space frame, clad to make it a whole continuous element enabling one to walk on it and put a certain load. Another apt example of Pillow Space Frame’s unique capabilities is the hangars commissioned by Mediterranean Aviation Company Ltd. Pillow Space Frame Ltd. were awarded the contract for the design, manufacture and construction of these hangars, including ancillary offices, hangar doors and remote controlled apertures. Whilst not having the same load capacity as predalle constructed buildings, such structures allow for photo voltaic panels to be installed as well as maintenance to be carried out.
The choice between predalle or steel really depends on the function of the roof. For example, Martin continues to explain, the Wasteserv facility in Gozo was built in a quarry.

The major challenge in this project was the total length of the runner beams of one running mile, which all had to be installed simultaneously while other service providers were working at the same time.
Thus, the use of steel can even be accompanied by concrete in order to retain, and amplify, the advantages enjoyed by the more traditional building methodologies.
Investing in Technology
Fully aware that this type of construction is not a straight forward plug and play process, Pillow Space Frame invested in sophisticated tools from the very beginning.
steel is not variable, as concrete is; the value of its strength is constant
Whilst concrete suppliers have their own laboratories to ensure that the load being undertaken conforms to industry certification, steel does not require such testing. This is because steel is not variable, as concrete is; the value of its strength is constant. This does not mean that it is not certified, however the process takes place prior to the actual purchase – This is very similar to when you are buying a car- you know that it is certified.
Notwithstanding, or perhaps because of the changes which the building and construction industry is currently undergoing, the feeling is that there is an even brighter future for space frames on the island. With such materials satisfying the requirements for economic, safe and speedy construction, it cannot be long before it is the industry at large which will tap into its full benefits and potential.
Pillow Space Frame’s collective mindset is a pioneeral one; outright leaders in their field and not adverse to change. It will lend itself well to the proliferation of additional developers seeking their help.
Comment