Model making, prototypes design, Rapid Tooling & Jig Design, and general product design and development all form part of Invent 3D Limited’s extensive portfolio of products and services made available to Malta’s construction, property and interiors industries. Whilst today Invent3D has made a name for itself as a leading partner for all such matters of design and making, much like many of the world’s leading businesses of the likes of Apple and Amazon, the company’s origins stem from a garage operation too.
Fast forward to present time and the company now operates from its new premises located on the Mriehel Bypass, in Qormi, which houses a team of 11 staff members. These include engineers, technicians, designers, free-form designers (for sculpting), engineering designers, and electronics engineers. The newest addition to the team is a Sales Manger, who joined the company only a few weeks ago, with the purview of settling the company within the higher tiers of brand positioning where it rightfully deserves to reside.
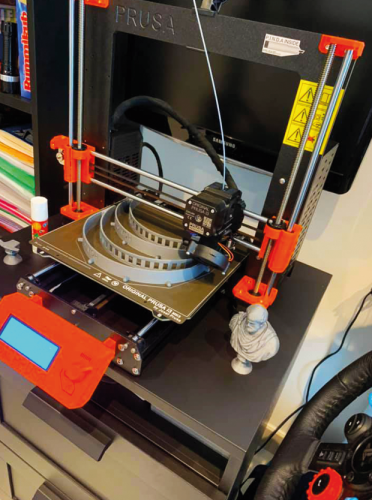
Beyond being business partners, the co-founders David and Alexandra Sciberras share their surname as they have been married for 9 years and have three children together. David, who provides the technical input, is qualified as a warranted mechanical engineer, with a Masters degree in integrated product development, while Alexandra, who is the company’s Chief Operations Officer, is a pharmacist by education and has injected into the company the obsessive focus on quantities and measurements that her profession advocates.
David started developing a passion for 3D printing when he was working with Toly Products as an innovation engineer in the cosmetics sector. His interest rapidly intensified and he purchased his first 3D printer from China as an impulse buy for his birthday, 6 years ago. He set out feelers to see whether his hobby could be monetised by starting a Facebook page promoting the car keychains he produced; he is also a car enthusiast. “Soon I was trying out different products and in no time I bought more printers. Around 20 3D printers had mushroomed all over our living room, at a time when our second child was also on the way,” he recounted.
The original client base was composed of car enthusiasts, as back then they were only making key chains and car parts. “Eventually we moved into more complex and innovative product ideas, which could be produced off-printer and were immediately available to the client as they are fast to design and manufacture,” Alexandra explained.
Alexandra … is a pharmacist by education and has injected into the company the obsessive focus on quantities and measurements that her profession advocates
By 2018, it became clear that there was serious potential to the venture and both David and Alexandra shifted to working for their newly founded start-up on a full-time basis and relocated their business operations out from their habitation zone and into a dedicated garage facility. David explained that prior to the advent of 3D printing, industry standards for coming up with new products entailed a time-frame of between 6 and 12 months. “Now, launching a new product on the market requires a time-frame of six to twelve days tops – with environmentally friendly low-waste products, made from recycled plastic,” he added.
“we moved into more complex and innovative product ideas, which could be produced off-printer and were immediately available to the client”
The company is able to provide clients with customised products which do not warrant mass production or even bulk importation. In addition, David explained that “Invent 3D Ltd makes use of plastics that are high strength – in some cases close to the strength of aluminium – to produce tooling and jigs. We use reinforced plastics, using Kevlar and Carbon Fiber, to make this happen. Knowing what materials to use in the right situation is critical to the success of the product.”

In a nutshell, then, their client presents an idea, and they produce it; transforming a simple concept into a tangible tool or model. “We have tested nearly every niche on the Island and products which are successful are then internationalised and packaged for global resale. An example of this is our merchandising products which have proven to be very successful and which we have launched internationally last year,” Alexandra enthused. Similar success has also been achieved by the company’s unique trophies, which too are made of sustainable plastic.
“Invent 3D Limited makes use of plastics which are stronger than aluminium or steel, to produce tools from kevlar and carbon fibre”
Invent 3D Ltd’s clientele has expanded to now include the architectural sector, as well as the biomedical and cosmetic industries, scale modelling and a host of components for products in pest control, spare parts for cars, tools for the construction and manufacturing industries, as well as toys. The company also manufactures vital parts and mechanical components which are no longer in production.

The company currently imports the recycled plastic it uses to manufacture its products and plans are underway to house a full recycling centre in the basement of its new premises. “This will enable us to have an in-house full circular economy, with a zero-waste policy for our manufacturing plastic footprint. We will even be able to recycle construction waste (like sand and cladding) that can then be blended with a polymer and to revive recycled wood and plastics via modern print designs,” David proudly explained. It seems to me that apart from the obvious advantages of making use of their services, developers ought to include Invent 3D as part of their CSR endeavours and campaigns.
Invent 3D Limited’s clientele has expanded to now include the architectural sector, as well as the biomedical and cosmetic industries, scale modelling and a host of components for products in pest control, spare parts for cars, tools for the construction and manufacturing industries, as well as toys
David outlined the typical service which Invent 3D offers architects, particularly for the design of scale models of buildings and projects. “The architect sends us the renders or plans of the project and we provide the sales model (which can be used for financing, sales and logistics purposes) or the trophy model, for the CEO or Board’s use. Our scale models are of international quality and are very helpful in supporting the architect’s end clients to visualise the job,” he explained, adding that the company is currently working on scale models for projects in Dubai, South Africa and Sicily.
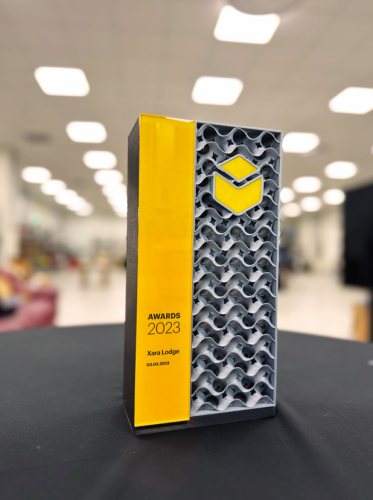
by Invent 3D
The company also produces custom furniture and custom parts. “We have interior designers who come to us to produce unique pieces for them, or items that are not usually done. We can do these on a one-off basis or we can mass produce them, depending on the client’s requirements,” David added. Invent 3D has the in-house technology to manufacture a client’s design on an exclusive basis. “Other manufacturers can require minimum order quantities running into the tens of thousands, however we can produce single digit quantities to order. We handle the design and manufacturing elements, with the Intellectual Property of the item typically resting with the client,” he elaborated.
Not known for sitting on their laurels, both David and Alexandra have a strong vision for the company’s future, which includes metal and clay printing, both of which will require separate machinery. They are looking to scale up their business yet further and seek out more innovative ways of applying their technologies which enables Invent 3D Ltd to print and produce anything from furniture to a cog.
“Overseas they are already printing houses – bungalows with recycled plastics, so there is still immense untapped potential locally for 3D printing. In the near future we are planning to set up a 2m x 2m x 6m printer that would be able to print a boat,” David added enthusiastically.
Comment